Entretien avec Damien Gasse de Novacarb
Entretien avec Damien Gasse, responsable des ressources minérales pour la filiale Novacarb
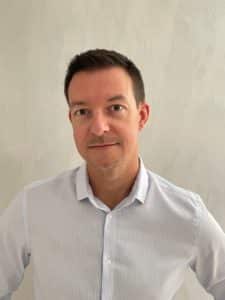
Cavités salines, relevés au drone et études écologiques : entretien avec Damien Gasse
Nos salariés ont du talent
Bonjour Damien, peux-tu commencer par te présenter ?
Je suis Damien Gasse, ingénieur géologue, aujourd’hui responsable du service Matières Premières et membre du Comité de Direction de l’usine Novacarb de La Madeleine, près de Nancy (France), pour le Groupe Humens.
Le rôle de mon service est d’assurer la disponibilité, l’exploitation et l’acheminement jusqu’à l’usine des ressources minérales essentielles pour notre activité. En effet, nous sommes intégrés sur les matières premières qui rentrent directement dans le procédé de production de nos carbonate et bicarbonate de sodium : le sel et le calcaire. Nous exploitons ces ressources minérales sur deux sites : une carrière de calcaire à ciel ouvert et un champ salin relevant du régime minier… ce qui explique la présence d’une équipe de géologues chez Humens ! Nous avons également la charge de la gestion et de l’exploitation des bassins de traitement des effluents de l’usine. Nous intervenons donc en amont et en aval du procédé !
Comment es-tu arrivé chez Novacarb ?
J’ai fait mes études à Nancy, d’abord à la Faculté des Sciences et Technologies puis à l’Ecole Nationale Supérieure de Géologie. Je me suis spécialisé en géologie minière, notamment en exploration, et j’ai effectué mes stages pour la prospection d’or dans l’Anti-Atlas marocain ou d’uranium dans le désert de Gobi. Ces premières expériences ont été déterminantes et m’ont conforté dans mon projet. Après avoir obtenu mon diplôme en 2007, je suis parti travailler en Irlande pour une société de service en exploration minière. A partir de ce moment, j’ai beaucoup voyagé ! J’ai sillonné l’Afrique pendant près de 10 ans au gré des différentes missions que l’on m’a confiées : Mauritanie, Angola, République du Congo, Soudan, Arabie Saoudite…
L’exploration nous emmène de plus en plus loin : je me suis souvent retrouvé dans des lieux très isolés, que ce soit dans la brousse, le désert ou la forêt, à plusieurs jours de la ville la plus proche. Si l’on ajoute à cela les échanges et le travail avec les populations locales, la vie de géologue est pleine de surprises.
Backpacker ! C’est une passion ?
On peut dire ça ! Je fais partie de la « génération Jurassic Park » qui rêvait de paléontologie, donc j’ai un penchant naturel pour l’exploration et la recherche... Finalement, mes études en géologie minière m’ont permis d’assouvir cet attrait pour les fouilles et la prospection avec une dimension économique en plus.
Après ces quelques années de formation sur le terrain et ces premières expériences réussies, j’ai cofondé la société de service, Afrex Geoservices, qui a compté jusqu’à 6 géologues. Notre grand succès a été d’identifier et de caractériser un très gros gisement de phosphates sédimentaires, en République du Congo.
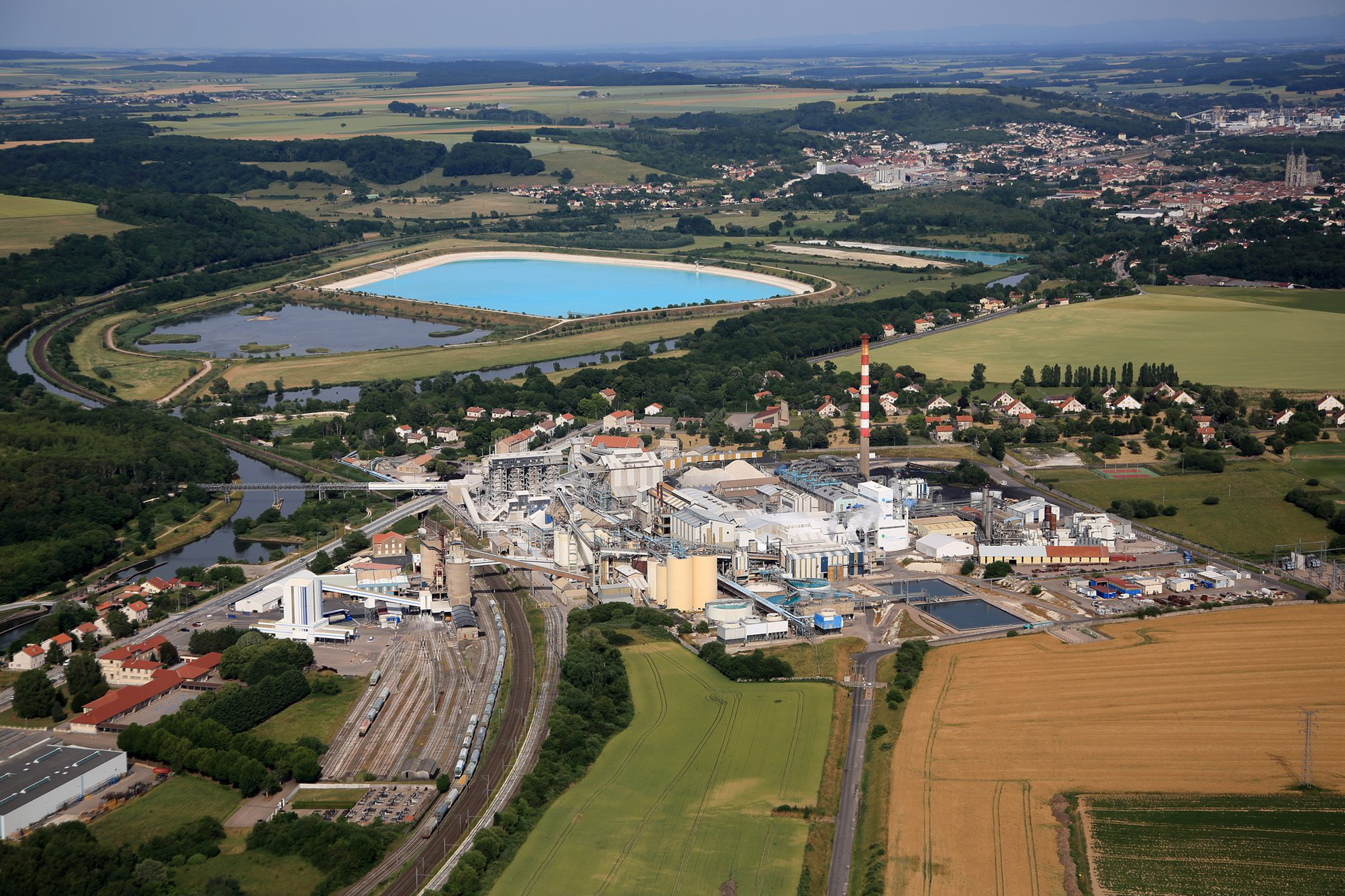
Usine de La Madeleine, France, et ses bassins de décantation des effluents du procédé
Peux-tu nous expliquer comment s’y prendre, pour trouver un gisement ?
Un client, qui s’était vu octroyer une licence d’exploration vers Pointe Noire, dans la plaine côtière du Congo, soupçonnait la présence de phosphate, un minéral essentiel pour produire des engrais. Nous avons analysé la bibliographie et les indices à disposition. Des décennies d’exploration et de forage pétroliers ont enrichi la banque de données des services géologiques nationaux, notamment celui du BRGM (Bureau de Recherches Géologiques et Minières) en France.
Sur cette base, et après avoir découvert les premiers indices de terrain, nous avons lancé un programme d’exploration composé d’analyses géochimiques et géophysiques puis de forage de reconnaissance lorsque les premières cibles ont été identifiées. Une fois que les contours du gisement et ses caractéristiques ont été compris, nous avons passé plusieurs années à forer en resserrant de plus en plus la maille de forage : d’abord tous les kilomètres, puis tous les 500 mètres, puis tous les 250 mètres, etc… Une fois le gisement délimité, des méthodes géostatistiques sont ensuite mises en œuvre pour quantifier les ressources, en termes de tonnage et de teneur. Plus la maille de forage est fine, plus la classification des ressources est bonne, ce qui permet de les convertir plus tard en réserves minières lorsqu’une étude de faisabilité du projet est produite.
Mon travail s’est arrêté là, sur ce chantier. Après 5 ans avec Afrex Geoservices, c’était aussi le bon moment pour moi pour rentrer en France. Rejoindre NOVACARB, dans ma région d’origine, était une aubaine après tant d’années à l’étranger : j’y suis entré en 2016 comme responsable de l’exploitation saline et des bassins de décantation des effluents de l’usine. En 2017, mon poste s’est étendu à la gestion de notre carrière de calcaire, située dans la Meuse, et à la réception et au traitement des matières premières minérales à l’usine. Depuis, j’ai également intégré le comité de direction du site.
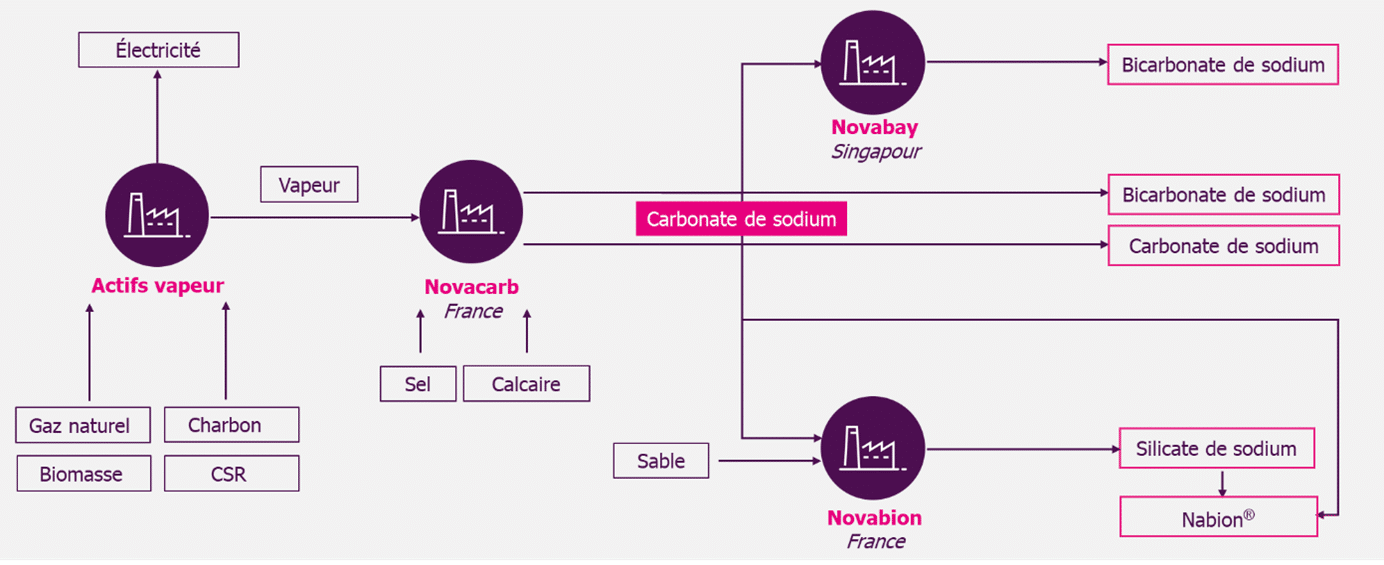
La chaîne de valeur du groupe Humens
Commençons par le calcaire : d’où vient-il ?
Celui que nous exploitons à la carrière du Revoi, située à Pagny-sur-Meuse, provient de niveaux géologiques datant d’environ 160 millions d’années, une période du Jurassique Supérieur que l’on appelle l’Oxfordien. A cette époque, sous nos latitudes, la région bénéficie d’un climat chaud et sec. La mer est présente à Pagny et on trouve un environnement de plate-forme carbonatée récifale, avec des milieux ouverts aux vagues et des zones de lagunes.
Dans ce milieu, les organismes marins respirent, ce qui fait précipiter les ions calcium dissous (Ca2+ + 2 (HCO3–) ↔ CaCO3 + CO2 + H2O) : les boues carbonatées se déposent sous forme de calcaire.
Fréquemment, on retrouve dans ces dépôts d’autres éléments dits terrigènes (silice, aluminium, fer) issus de l’érosion des continents, mais la production carbonatée est telle dans la zone à cette époque qu’elle comble l’espace disponible ne laissant pas d’espace pour l’accumulation de produits détritiques. Ces conditions propices aux dépôts sédimentaires nous permettent aujourd’hui d’extraire un calcaire très pur, supérieur à 99% en CaCO3.
On y retrouve d’ailleurs une grande quantité de faciès et de fossiles, ce qui fait le bonheur des sédimentologues et des paléontologues de l’Université de Lorraine !
Lien : Description géologique de la carrière du Revoi sur le site de l’Académie Nancy-Metz
Il ne s’agit donc pas d’extraire du produit fini ?
Non ! Il existe des gisements de carbonate de sodium naturel, qu’on appelle Trona, mais ils sont rares en Europe. Les plus gros gisements sont situés au Wyoming (USA) ou, plus proche de chez nous, en Turquie dans la région de Beypazari. Le Trona contient davantage d’impuretés (métaux…) que le carbonate de sodium synthétique que nous produisons par un procédé de chimie minérale à l’usine de La Madeleine.
Les unités de production de carbonate et bicarbonate de sodium (Na2CO3 et NaHCO3) se construisent toujours près d’un gisement de sel (chlorure de sodium, NaCl). Avec le calcaire (carbonate de calcium, CaCO3), ce sont les deux ressources minérales de base du procédé de fabrication.
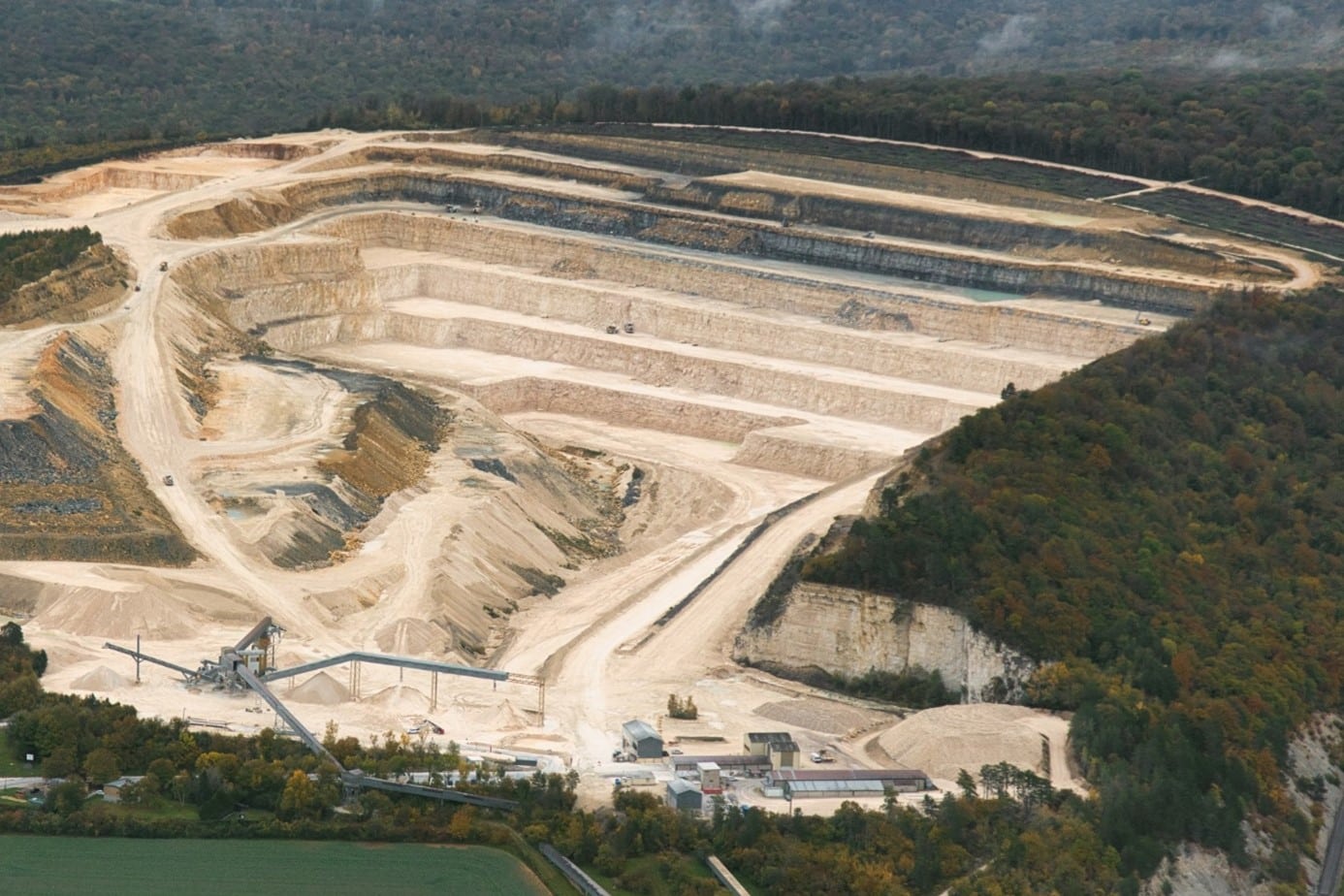
Vue aérienne de la carrière du Revoi de Novacarb (Novacarb, 2023)
Les techniques d’exploitation se modernisent ?
Oui : nous extrayons environ 1,5 Mt/an de calcaire dont une large fraction alimente les fours à chaux de notre usine de La Madeleine qui produisent le CO2 et la chaux nécessaires au procédé. Cela demande une grande quantité de travail mécanique, et mobilise beaucoup d’engins de carrière. Optimiser les pratiques prend donc tout son sens.
Effectuer des relevés du site par drone est entré dans nos pratiques courantes : les images obtenues sont géoréférencées et un traitement est réalisé par photogrammétrie pour obtenir des modèles numériques de surface qui permettent d’accéder facilement aux volumes de matériaux abattus. Les drones peuvent aussi être utilisés pour cartographier les fronts de taille et leur rugosité, ce qui permet d’ajuster les charges explosives et d’aller toujours plus loin dans l’optimisation. Nous y avons recours parfois.
Des progrès sont aussi réalisés dans le suivi des engins, à la fois à travers les données qu’ils transmettent automatiquement et qui sont accessibles en ligne sur un cloud, et par le biais de leur géolocalisation. Nous obtenons désormais facilement des données statistiques sur les tonnages transportés, sur les durées des cycles de rotation des engins, sur les défauts, etc. L’analyse de ces données permet d’identifier les points d’arrêts et les ralentissements, que ce soit en carrière ou sur les installations de traitement. Ce sont les prémices d’une démarche de « learning system », pour identifier les points bloquants.
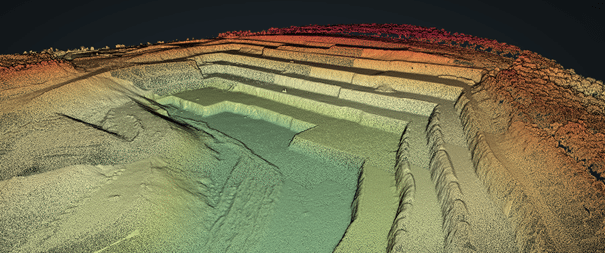
Modèle numérique de surface de la carrière de Pagny-sur-Meuse créé par traitement photogrammétrique des photographies aériennes au drone (Novacarb, 2024)
Qu’en est-il de l’exploitation du sel, la deuxième ressource minérale ?
Notre concession de Lenoncourt doit fournir plus de 300 m3/h de saumure saturée en sels, et ceci en continu, 24h/24. Cela représente près de 800 kT d’équivalent sel gemme par an.
Le bassin de stockage d’eau salée brute situé à l’usine de La Madeleine n’offre qu’une autonomie très limitée pour le procédé de fabrication et il doit être alimenté en continu. Les enjeux sont primordiaux et nous avons une ligne d’astreinte dédiée à la surveillance et aux interventions sur les installations de l’exploitation saline en cas de problème en dehors des heures ouvrées sur la concession minière.
Quelle est l’histoire de ce sel ?
Il faut remonter encore un peu plus dans le temps, jusqu’au Trias Supérieur, il y a quelques 220 millions d’années. L’Océan Atlantique ne s’était pas encore ouvert et une mer, appelée Mer Germanique, était présente à l’Est.
A cette époque, une partie de l’est de la France se trouve en bordure de cette mer et Lenoncourt se situe dans une petite dépression, avec un seuil qui donne sur la mer. Quand le niveau de la mer augmente, la dépression se remplit d’eau salée ; quand le niveau diminue, la cuvette n’est plus alimentée : l’eau stagne, s’évapore et le NaCl se dépose. Cette couche a ensuite été recouverte par d’autres couches, marneuses, argileuses.
Le gisement de sel de Lenoncourt n’est pas très épais, de l’ordre de 150 mètres seulement (on trouve des couches de sels en Europe du Nord qui atteignent 1 km d’épaisseur) et nous n’exploitons que les trois faisceaux supérieurs qui totalisent environ 80 mètres de puissance, mais elle a l’avantage d‘être proche de la surface actuelle, à environ 220-300 mètres de profondeur. La couche de sel est encore plus proche de la surface dans les vallées environnantes, notamment celle de la Meurthe, et c’est pour cela que son exploitation a commencé au milieu du 19ème siècle.
Le sel à l’intérieur des terres (sur le site de l’Académie Nancy-Metz)
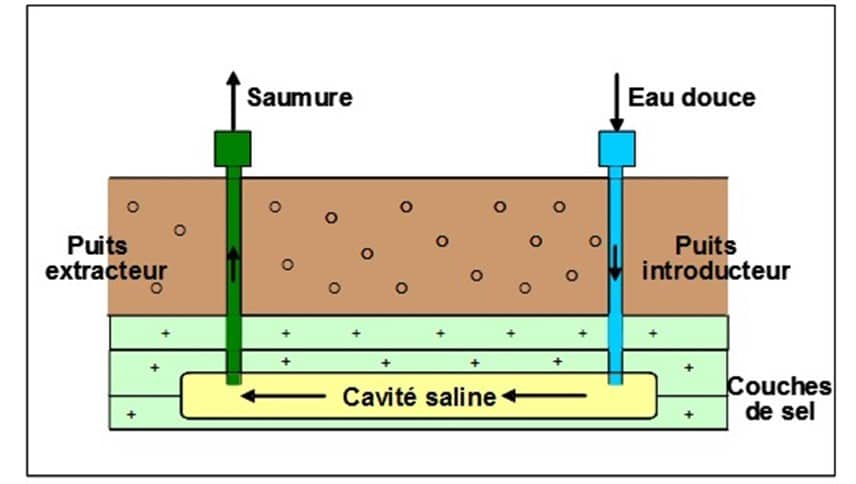
Schéma de principe de l’exploitation du sel par dissolution (Novacarb)
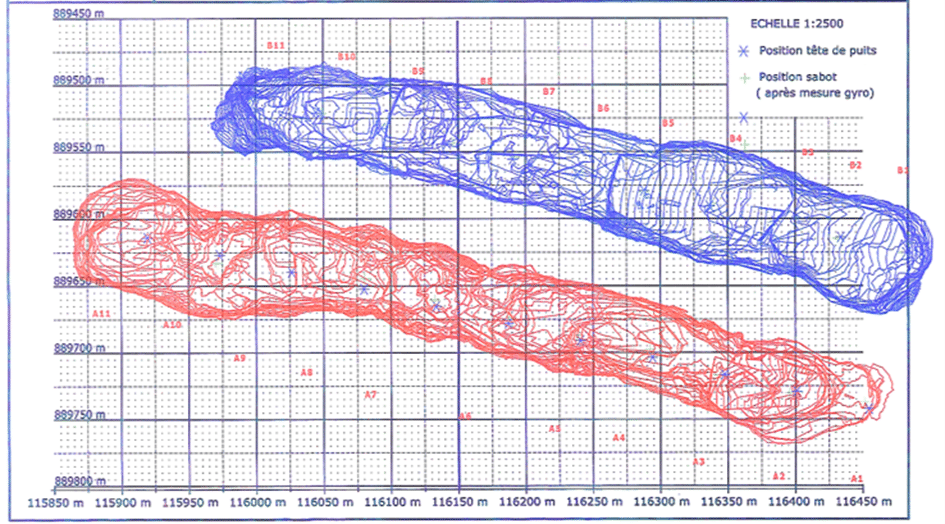
Cavités salines développées à l’aplomb des pistes A et B. Vue du dessus des formes déterminées par sonar. Chaque piste, constituée de 11 puits, fait 500m de longueur
Comment l’extrait-on ?
On extrait le sel par dissolution in situ, c’est la méthode de « solution mining », qui fait appel à des forages d’exploitation, appelés puits, reliés entre eux par des cavités et des couloirs de dissolution au sein du massif salifère. Certains puits sont introducteurs d’eau douce et d’autres sont extracteurs de saumure.
Historiquement, les puits étaient reliés entre eux par hydrofracturation, c’est-à-dire par injection d’eau sous très forte pression. La mise en pression d’un fluide incompressible provoquait la fracturation et le décollement des couches de sel et permettait de forcer la connexion entre les puits. Une fois la connexion établie, des circulations d’eau douce permettaient de créer des cavités et de transformer l’eau douce en saumure. Cette technique avait un gros inconvénient : s’il était possible de mesurer la quantité de sel extrait, on ne pouvait cependant pas savoir précisément quelle était la forme de la cavité sculptée ni l’évolution verticale de la dissolution au sein du massif. En conséquence, le défruitement était souvent trop important et les terrains de recouvrement perdaient leur stabilité, et donnaient lieu à des effondrements : nous constatons encore aujourd’hui sur notre site d’exploitation des effondrements résultant de cavités creusées il y a plusieurs décennies. D’ailleurs, ici aussi, nous utilisons des drones pour suivre la topographie du terrain.
L’arrivée de nouvelles technologies comme l’échométrie faisant appel à des sondes sonar, qui permettent de déterminer la forme des cavités, a permis d’améliorer la méthode à partir des années 90.
La technique de connexion des puits entre eux a également été largement améliorée. Désormais, un passage est formé dans une direction préférentielle en contrôlant la dissolution. En plus de l’eau douce, on injecte de l’air qui forme un matelas protégeant le toit de la cavité. L’eau douce, qui a une tendance naturelle à dissoudre le toit de la cavité du fait de sa plus faible densité, est alors forcée de se répandre sur les côtés, formant une cavité en forme de disque. En forant un puits tous les 50 mètres et en répétant l’opération, ces disques se connectent entre eux, afin de tracer une piste de forme contrôlée : c’est la phase de coalescence qui remplace complètement l’hydrofracturation.
In fine, les premier et dernier puits d’une piste sont équipés pour injecter l’eau douce et extraire la saumure. Pendant cette phase d’exploitation, d’autres sondes nous permettent d’évaluer l’épaisseur de sel résiduelle. Nous travaillons avec le centre de Géosciences de Mines ParisTech pour établir des modèles de stabilité géomécanique, et déterminer les formes et dimensions maximales des cavités permettant d’optimiser la récupération du sel tout en garantissant la stabilité des terrains surplombant les exploitations et s’affranchir de tous phénomènes d’effondrement.
Ce sont des projets conséquents.
Oui, nous développons depuis 2019 une nouvelle zone d’exploitation à l’est de notre concession minière. Ce nouveau champ salin comprendra à terme une centaine de puits et 5 cavités de grande longueur. Nous avons créé la première cavité entre 2020 et 2023 et venons de terminer les forages de la seconde, une piste de 850m de longueur. A ce stade du projet, plus de 10 millions d’euros ont déjà été investis pour pérenniser nos réserves minières en sel qui sont stratégiques.
L’obtention des autorisations pour démarrer des nouveaux travaux miniers prend plusieurs années. Il faut ensuite compter 8 à 12 mois de forage par nouvelle piste, puis environ 2 ans pour opérer la coalescence et créer la proto-cavité avant de pouvoir l’exploiter. Plusieurs personnes de mon service travaillent sur ces sujets et nous faisons appel à des prestataires extérieurs ainsi qu’au bureau d’étude de Novacarb pour certains aspects spécifiques à ces travaux neufs.
La durée de vie d’une piste dépend de sa longueur, en général l’exploitation dure entre 3 et 5 ans, donc l’opération doit régulièrement être renouvelée pour maintenir nos réserves.
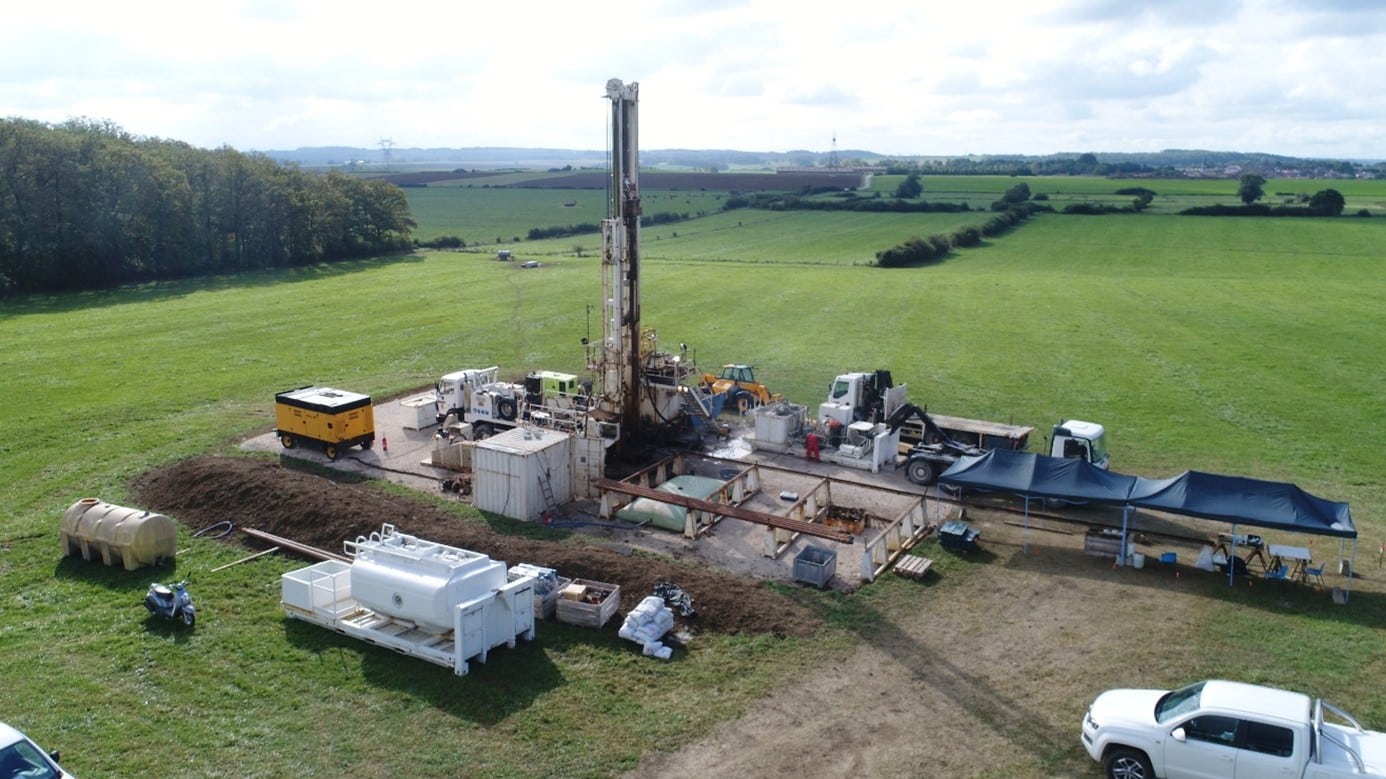
Forage d’un puits de reconnaissance sur la concession minière de Lenoncourt (Novacarb, 2023)
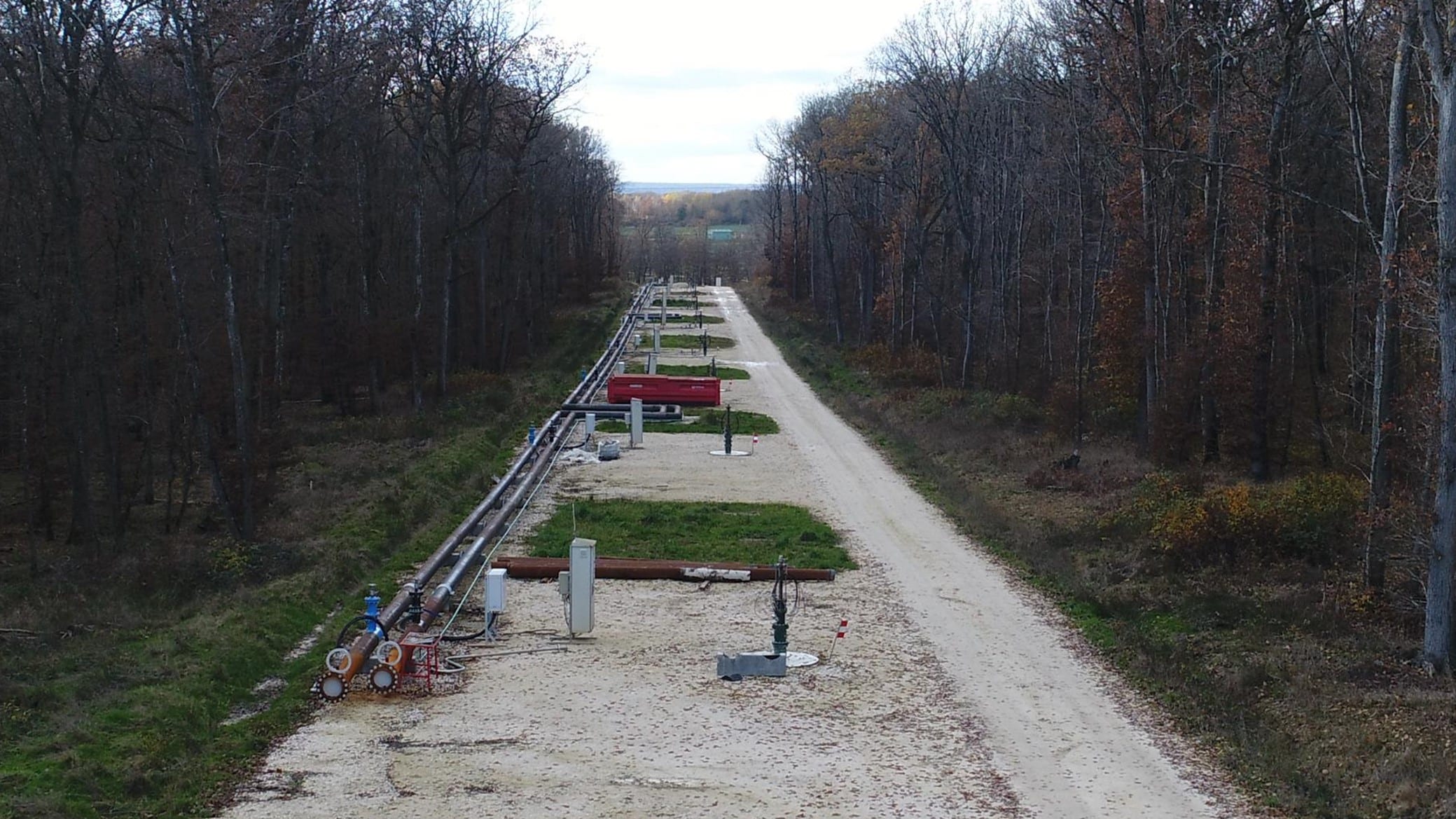
Piste d’exploitation en cours de développement sur la concession minière de Lenoncourt (Novacarb, 2023)
Pourquoi les phases d’autorisation sont-elles aussi longues ?
Car les aspects environnementaux sont primordiaux pour nos projets, et que l’évaluation des impacts et la définition des mesures environnementales à mettre en œuvre nécessitent souvent de longues études.
Nous avons installé, et continuons de développer au gré de l’extension de notre exploitation, un réseau de surveillance des eaux souterraines constitué de piézomètres pour suivre les niveaux des nappes aquifères et contrôler l’absence de connexion avec nos exploitations qui se traduirait par des teneurs en chlorures trop élevées.
Mais les enjeux environnementaux se jouent aussi en surface ! Une partie de l’exploitation se situe dans une zone boisée, et des défrichements sont nécessaires pour installer certains puits. Pour chaque nouveau projet, nous menons donc des inventaires pendant 2 ans en moyenne pour mesurer l’état initial de la faune, de la flore et des habitats afin de pouvoir ensuite évaluer l’impact de notre projet sur la biodiversité, et proposer la mise en place de mesures d’évitement, de réduction ou de compensation si nécessaire.
Nous travaillons aussi en partenariat avec les associations d’écologues afin de proposer des mesures d’accompagnement ou de suivi. C’est le cas par exemple pour les chiroptères (chauve-souris) pour lesquels nous avons mis en place des gites afin de développer leur présence sur notre exploitation ou des amphibiens pour lesquels nous avons créé des mares forestières. Les inventaires faune/flore annuels que nous organisons permettent de dresser chaque année un bilan de la fréquentation du site. Au cours du premier cycle triennal d’inventaire 2020-2022, pas moins de 119 espèces d’oiseaux ont été recensées sur la zone d’étude. 38 d’entre elles sont patrimoniales et 19 inscrites à l’Annexe I de la Directive européenne « Oiseaux ».
Parmi celles-ci figure un couple de Milans royal qui a installé son nid sur notre exploitation. C’est un rapace migrateur de grande taille, endémique de l’Europe de l’Ouest. En France, l’espèce est classée comme une espèce menacée donc l’arbre sur lequel il a élu domicile est bien préservé et mis sous surveillance !
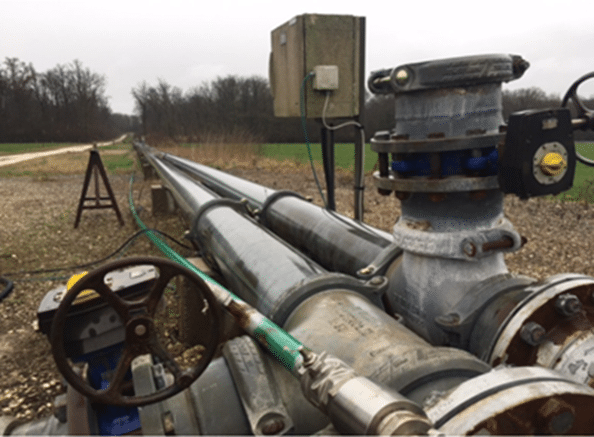
Collecteurs d’eau douce et de saumure le long d’une piste d’exploitation
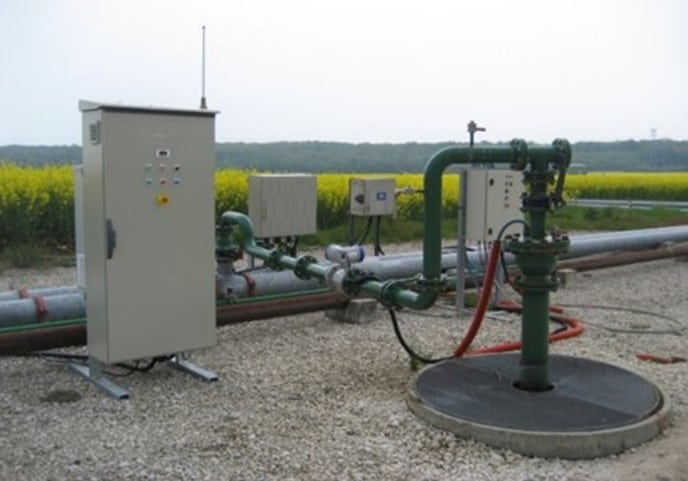
Puits d’extraction de saumure relié au collecteur de saumure
En conclusion, comment vis-tu le fait d’être géologue dans un Groupe peuplé de chimistes ?
Plutôt bien ! D’ailleurs il y a désormais des profils très variés dans le Groupe… en plus des chimistes qui restent bien représentés ! Et je ne suis plus le seul géologue, d’autres sont venus renforcer le service depuis ! Les missions requièrent beaucoup de technicité avec une approche multidisciplinaire pour traiter tous les aspects des nouveaux projets. Nous intervenons en amont du procédé de fabrication avec l’approvisionnement en sel et en calcaire mais également en fin de chaîne avec la gestion des effluents issus du procédés dans les bassins de décantation. C‘est le cas pour la partie réglementaire et administrative également, nous intervenons depuis la rédaction des dossiers de demande jusqu’à ce que les arrêtés d’autorisation soient signés.
Les taches sont variées et les enjeux différents d’un site à l’autre mais l’objectif commun de tous les secteurs composant le service Matières Premières reste bien sûr d’assurer que l’usine puisse produire en garantissant la sécurité autour de nos exploitations et le respect de nos prescriptions réglementaires, notamment environnementales. Il faut composer en permanence avec les aspects opérationnels, réglementaires et environnementaux, c’est un défi quotidien et la richesse du poste !
Merci Damien, un voyage du début à la fin !